Creating a Preventative Maintenance Program for your Commercial Laundry
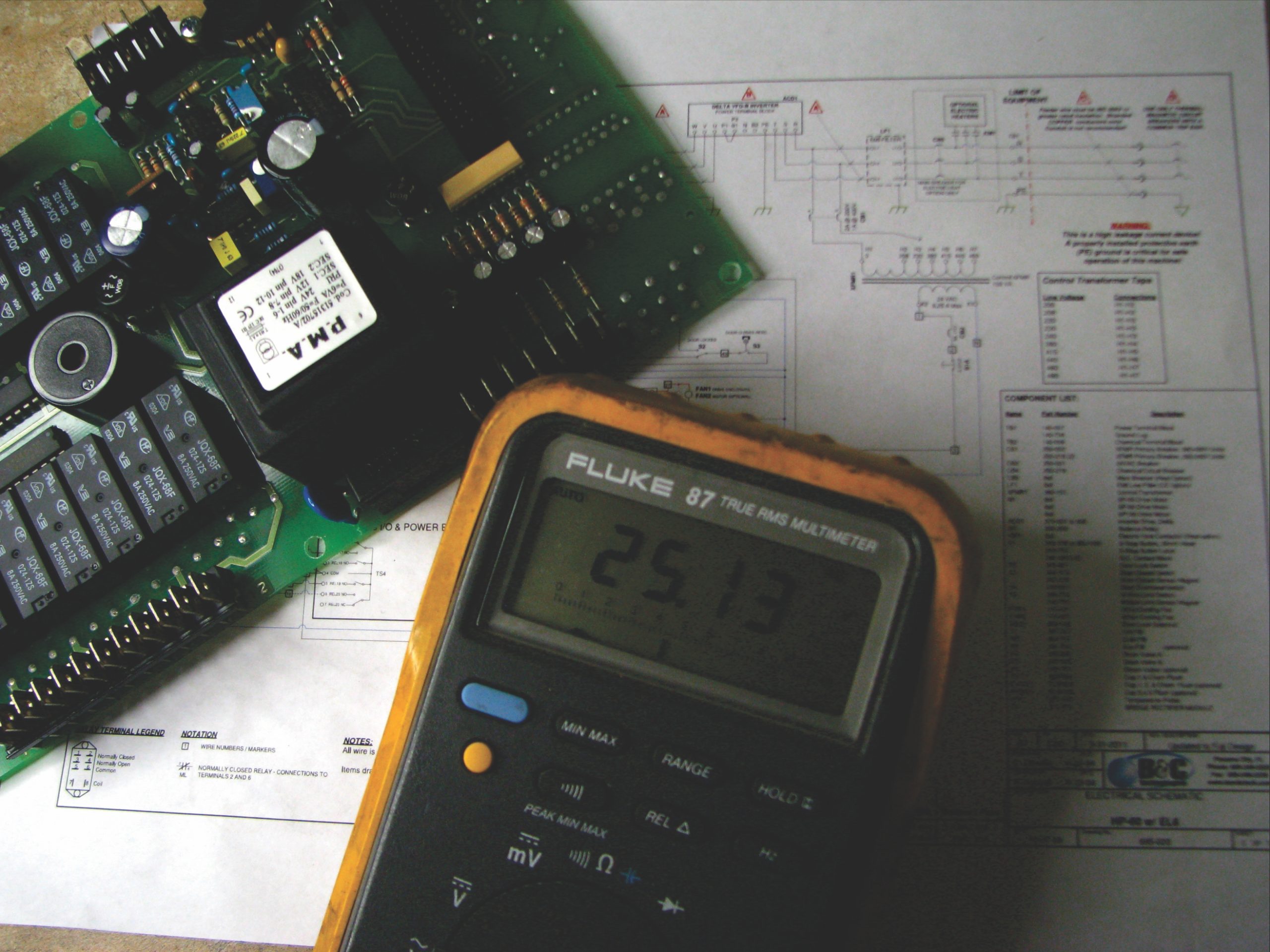
Creating a Preventative Maintenance Program for your Commercial Laundry
Performing routine maintenance on the commercial laundry equipment that companies rely on to produce clean goods and meet their customers’ tight deadlines may not sound exciting but it may well make the difference between meeting and missing a delivery date. Regularly scheduled preventive maintenance can uncover potential safety problems, enhance quality, save money by prolonging laundry equipment life, and optimize productivity by keeping machines fully functional and addressing equipment needs before they result in unanticipated downtime.
If you are considering implementing a preventative maintenance program (and you should be if you don’t have one in place), here are some guidelines for getting your PM program off of the ground:
- Schedule maintenance according to equipment usage
Although some machines prompt the operator to perform certain maintenance tasks, waiting until this happens can interfere with production. If tasks are scheduled in advance, they’re less likely to be postponed and then forgotten in the interest of meeting a production deadline. The more you use a machine, the more abuse it takes, so plan machine maintenance frequencies accordingly. If you run a small washer eight hours a day, a maintenance schedule of once every three months is probably adequate for that machine. But if you’re running three shifts on the same machine, you might need to perform maintenance tasks on it once every month or even more frequently if you don’t have a qualified maintenance crew. - Make employees accountable for maintenance
Once you’ve identified what preventive maintenance activities need to be performed and when they should be done, assign follow-through responsibility to a maintenance coordinator, machine operator, or other appropriate personnel. Have these designated employees sign off on maintenance activities on a sheet attached to each machine, through a software program, or through daily, weekly, and monthly cards submitted to supervisors. Whatever method you decide on for tracking, consistently follow the preventive maintenance schedule that you’ve devised. - Ensure that the preventive maintenance tasks being performed are beneficial to the equipment
Use the operating manuals for the machines to determine the maintenance tasks that need to be performed. Each piece of equipment is different and will have different maintenance requirements. Trying to use a catch-all technique will likely cause more problems. If you’re unsure which tasks are beneficial to each piece of equipment, ask your equipment representative. - Plan ahead to accommodate seasonality
Production need not suffer in order to perform preventive maintenance. Schedule tasks that require downtime during slower seasons. Typically, good machine maintenance can take a few hours, but this investment can prevent up to 48 hours of unexpected “corrective” maintenance when something breaks. - Ask your equipment provider for a maintenance arrangement
Most machinery distributors offer preventive maintenance service visits for a flat rate or for discounted parts and labor costs. If your provider doesn’t offer service agreements, propose a plan. Not only do service contracts help ensure that maintenance is performed on your equipment, but they also help you budget for it. Because maintenance programs are especially important for frequently used equipment, consider service programs for these machines at least. - Buy spare parts before they are needed
Ask your equipment provider for a recommended spare parts list. You need not buy everything on the list, but when service technicians are in your plant, ask what they recommend that you keep in your stock. The most needed parts usually can be purchased inexpensively, minimizing downtime when they are needed. - Let employees learn from equipment service personnel
When a technician is working on a machine, have appropriate personnel watch and ask questions. After a few visits with a service tech, your operator may be able to troubleshoot, fix simple problems, and know when to call for expert help. The technician can tell you which preventive maintenance procedures your operator may be competent to safely perform. - Document service visits
When you schedule a maintenance visit, make sure that the service tech will record the inspection. It is important to document not only the date of service, but also what parts of the machine have been checked and what service was performed. Have the rep provide a copy of the inspection record. This checklist will function as a record of service performed and will help you identify items your employees should be inspecting regularly on their own. - Keep service manuals handy
Manuals are often misplaced, but it is critical for machine operators to have access to them. The manuals contain valuable information such as schematics, parts identification, operational instructions, safety guidelines, and cleaning recommendations. Most manuals have a maintenance section detailing what should be done and at what frequency. This type of information is especially important to operators who were not around for the machine’s original training session. - Ensure that management is committed to preventive maintenance
Failing to schedule preventive maintenance, overriding scheduled maintenance in order to meet production needs, and asking employees to keep maintenance costs down can send the wrong message, and ultimately cost an organization more in terms of machine downtime and repair expenses. If production needs don’t allow for scheduled maintenance tasks to be executed, consider having the equipment maintained during off hours. When considering budgetary needs, realize that failure to perform preventive maintenance may result in much higher costs if equipment breaks down, particularly during a busy production time.
Preventative maintenance plans are worth the investment of time and energy because they help to predict the future. You can’t always tell when X, Y, or Z will happen, but a good plan will ensure a proactive strategy for preventing problems, funding improvements, and enhancing your laundry assets.
Antony Agok
May 11, 2021 - 5:20 am
Great! I do read this blog it helps me as a technician
Al Adcock
May 11, 2021 - 8:31 am
Thanks for the kind words and for reading the blog, Antony!