Building Efficient Wash Processes in your Commercial Laundry
Improving the efficiency of your commercial laundry can often be found in the details of the laundering process itself, receiving, sorting, washing, drying or ironing, and the preparedness and training of the staff.
Efficient washing generally has 4 aspects:
1. Temperature
2. Time
3. Chemicals
4. Mechanical Action
In order to wash at the highest efficiency, all of these factors must be in balance, and this balance has changed since it was developed in 1959 by Dr. Herbert Sinner.
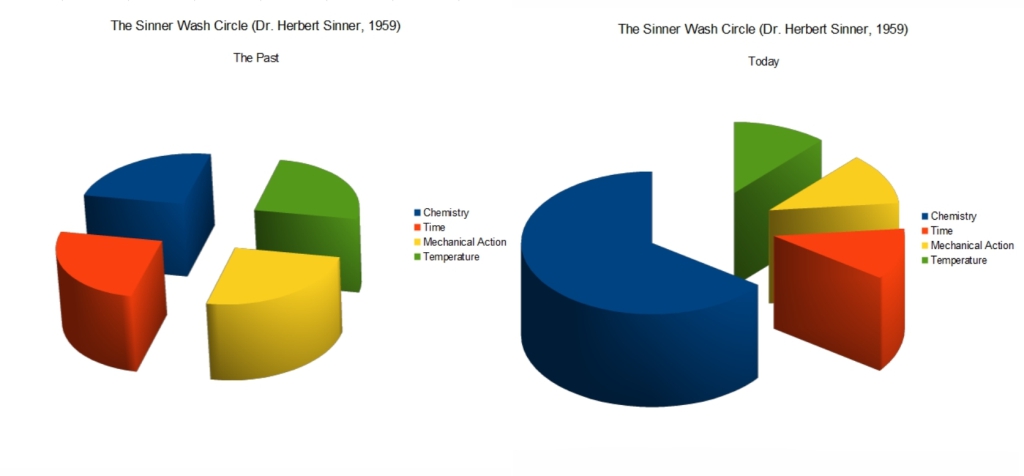
- The temperature plays a direct role in removing stains from the laundry, as well as killing germs. Hot water is a better solvent than cold water.
- The washing time is important as too little time in the wash will not allow proper stain removal, while too much time reduces productivity and reduces the life of the goods.
- Chemicals work with the water, and in general are made up of:
- A detergent (containing a surfactant, which lowers the surface tension of the water in effect making it wetter) which attacks and dissolves stains
- A bleach, which whitens fabrics, removes stains, and acts as a disinfectant
- A sour, which is slightly acidic and neutralizes the pH of the bath (improper pH causes yellowing in the dryer)
- A softener, which coats the goods with a thin layer of chemicals that provide lubricating properties and are electrically conductive, making the fabric feel smoother, preventing the buildup of static electricity, increased resistance to stains, and reducing wrinkling and pilling of the fabric. However, fabric softener should never be used if the goods will be processed in an ironer.
- Mechanical action forces the chemical and water solution through the fibers of the fabric, which removes the stain from the fabric, dilutes it, and carries it away.
Typically, a wash program has a wash bath followed by 3 rinse baths, with the final rinse containing the sour or softener. If the goods are especially soiled, a prewash bath is added, and for other highly stained goods, longer baths with higher temperatures and higher concentrations of detergents and bleaches are used.
Another factor that greatly impacts washing efficiency is fill and drain times. If the site of the laundry has poor water volume and pressure or undersized water supply lines, the fill times will be long. This can add up rapidly and increase the time for a wash load to complete significantly. The same logic applies to drain sizing. If the machine is tied directly into an undersized or slow flowing drain, it can add many minutes to the drain step each time a drain is required adding significant time. In the extreme case where the fill and drain is slow, cycle times can easily double which destroys the efficiency and throughput of the laundry.
Drying efficiency is also an important factor to consider. Extensive exhaust runs or undersized gas or steam supply systems can greatly increase the amount of time required to dry the goods. This is compounded on machines without humidity sensing systems, as overdrying of the goods is common. Humidity sensing allows the dryer control to measure the amount of moisture remaining in the goods and stop the drying process when a target moisture level is reached. This eliminates wasted time and wasted fuel, increasing the productivity of a laundry as well as decreasing the direct cost of fuel, a significant part of the cost of each load.
Efficiency of a deep chest ironer is directly affected by the fit of the padded roll into the chest, and the proper alignment of the roll as it fits into the chest. If the padding is undersized, only a small area of contact is created between the roll and the chest where the padding meets the chest. Likewise, if the padding is oversized, the roll cannot sit completely down into the chest, creating contact at the front and back of the chest. Maximum efficiency is realized when the padding is perfectly sized for the chest, allowing full contact while the goods travel through the machine.
Finally, trained operators and maintenance personnel are essential to the efficient operation of the laundry. Without proper maintenance, the machinery cannot be expected to operate at peak efficiency. Likewise, without trained operators, efficiency will suffer directly.
With these simple guidelines, the efficiency of a commercial laundry can be both measured and improved. After all, how can you know if your improvements are working if you aren’t measuring and comparing your before and after figures?